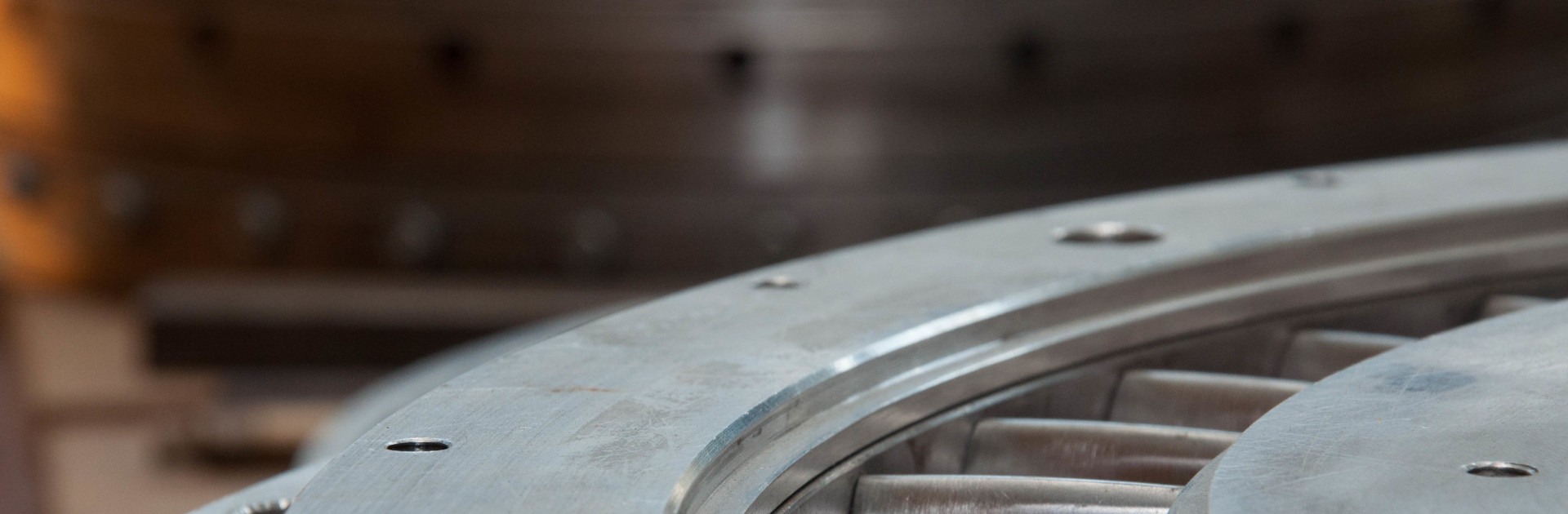
Energy engineering Laboratory
Numerical Methods
The research group focuses on mathematical modelling of fluid flow and heat transfer, including simulations of multiphase flows and multiphysics problems such as absorption/adsorption and more. These analyses range from conceptual 1D calculations to 3D simulations verifying the functionality of proposed prototypes.
1D balance calculations are performed as design calculations for thermal cycles and as simulations of transient processes during off-design operation of equipment. These simulations are also used to analyse the behaviour of individual components, for which we develop our own computational codes.
Advanced methods of numerical simulation of fluid flow and heat transfer are employed to optimize the real-world design of equipment and products to enhance desired properties, such as improving efficiency or reducing pressure losses.
CFD simulations are also used to verify proprietary in-house computational codes, which are derived for specific equipment and tailored to customer requirements. These codes are then implemented into standalone software, providing customers with a reliable, fast, and efficient tool for designing their equipment without the need for time-consuming 3D simulations at the conceptual design stage.
Tools
- MATLAB
- ANSYS (Fluent, CFX Mechanical, etc.)
- FlowMaster
- Tecplot
Experimental Methods
The research group focuses on theoretical and experimental studies of turbulent flows in both internal (channel and pipe flows) and external (body flow) aerodynamics.
We conduct highly precise measurements of flow fields using various experimental methods. The results allow for the evaluation of up to three velocity components, pressures, and temperatures. The final outputs may include velocity field statistics or flow rate assessments.
Additionally, we perform calibrations of anemometric probes using our highly accurate calibration equipment, which operates within a velocity range of 1 to 160 m/s. The calibration process takes into account airflow velocity, direction, and temperature. We utilize a highly precise positioning system with an angular adjustment accuracy of 0.1° for two angles.
We also analyse the characteristics of turbulent flows from experimental data, including mean values, statistical moments of velocity fluctuations, and correlations. The results may include quantities used in turbulence modelling to define boundary conditions for CFD calculations or validate the results of such computations, such as turbulent kinetic energy or dissipation rate. Furthermore, we evaluate specific turbulence characteristics, such as length scales (energy-containing, Taylor, Kolmogorov scales) or turbulence isotropy characteristics.
Equipment
- Optical system for measuring velocity fields (PIV), with 2–3 velocity components evaluated.
- Point velocity measurements at high frequencies (up to 100 kHz) using the hot-wire method (HW).
- Optical point velocity measurement using Doppler anemometry (LDA).
- Precise pressure measurements, flow evaluations, and specialized pressure probes (multi-hole).
- Calibration equipment for velocity and directional probe calibrations.
- Equipment for precise force measurements (aerodynamic balances).
- Measurement of temperature dependencies.
- Aerodynamic tunnels and tracks for high subsonic speeds.
- Software for data acquisition, evaluation, analysis, and presentation (LabVIEW, MATLAB, Tecplot, DynamicStudio, and others).